Strand Casting
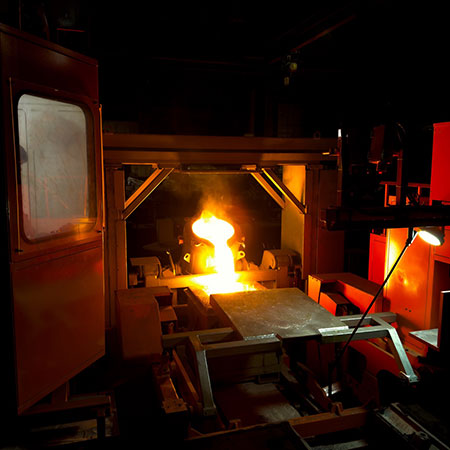
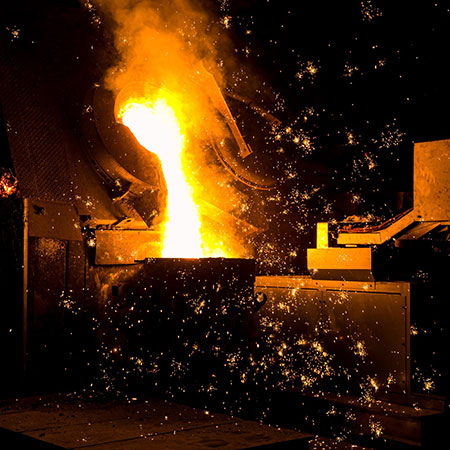
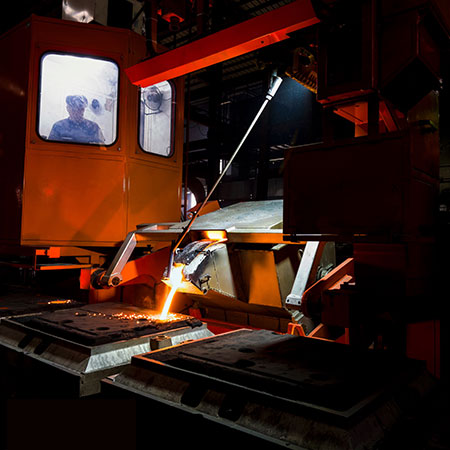
Continuous Casting Introduction
Our automated foundry integrates advanced equipment with smart manufacturing concepts, fully implementing automation processes from molding to finished product shipment. This creates a highly efficient, high-quality, and stable casting production environment.
Through a highly integrated system and real-time monitoring mechanisms, we have built a smart casting production line with international competitiveness.
1. Fully Automatic Molding System
Using FBOX and HSP fully automatic molding machines, we can quickly and stably complete mold formation:
• Precise control of mold compactness and dimensional accuracy
• Automated mold handling system with no need for manual operation
• Quick mold switching, enabling flexible and diversified production
2. Intelligent Molten Iron Handling System
• Molten iron is produced by high-frequency induction furnaces, equipped with automatic temperature control and composition monitoring.
• Molten iron transport cars operate entirely on tracks, precisely delivering iron to the pouring stations.
• Built-in temperature control and tipping monitoring during transport prevent heat loss and operational risks.
3. Automatic Pouring System
• Servo-controlled pouring equipment precisely controls pouring volume and speed.
• Equipped with visual and infrared sensors for real-time adjustment of pouring parameters, ensuring pouring stability and complete filling.
• Full automation recording of the pouring process for easy tracking and quality analysis.
4. Automatic Cooling and Mold Conveyance
• After pouring, molds enter an automatic cooling zone with cooling times automatically set according to product characteristics.
• The intelligent conveyor chain system transports molds without the need for manual handling, improving process efficiency.
5. Automatic Shakeout and Mold Dismantling
• After cooling, molds proceed to the automatic shakeout system, which separates sand and castings through vibration and rotary drums.
• Forms a closed-loop system with the molding machines, recycling and regenerating used sand to enhance resource utilization.
6. Casting Cleaning and Surface Treatment
• Castings are automatically sent into a shot blasting machine to remove oxide layers and sand residues.
• Robotic loading and unloading system: Robots automatically grip and transfer castings to grinding machines and unloading zones, integrated into the continuous production line.
• Robotic automatic grinding: Equipped with multi-axis freedom, robots automatically polish, deburr, and finish surfaces based on different casting shapes and requirements.
• Vision-guided system: Robots are equipped with vision recognition modules to automatically identify grinding locations and paths.
• Unmanned operation: The entire line operates through an automatic scheduling system, enabling 24/7 stable production and reducing manual intervention and labor safety risks.
• Stable product quality: Grinding parameters can be stored and replicated to ensure consistent surface quality and machining accuracy for each product.
7. Automatic Inspection and Quality Control
• Each batch of castings undergoes sampling inspection with fully automatic 3D coordinate measuring machines, ultrasonic flaw detectors, and hardness testers.
• Data is fed back to the central system for real-time process adjustments and problem alerts.
• Complete production traceability is established, complying with ISO quality systems and customer traceability requirements.
Overall Advantages of Automated Casting
• High automation reduces human risk and costs.
• Smart monitoring enhances product consistency and traceability.
• Modular design allows for flexible manufacturing capabilities.
• High production efficiency ensures stable lead times, supporting both mass production and diversified small-batch production.