Introduction
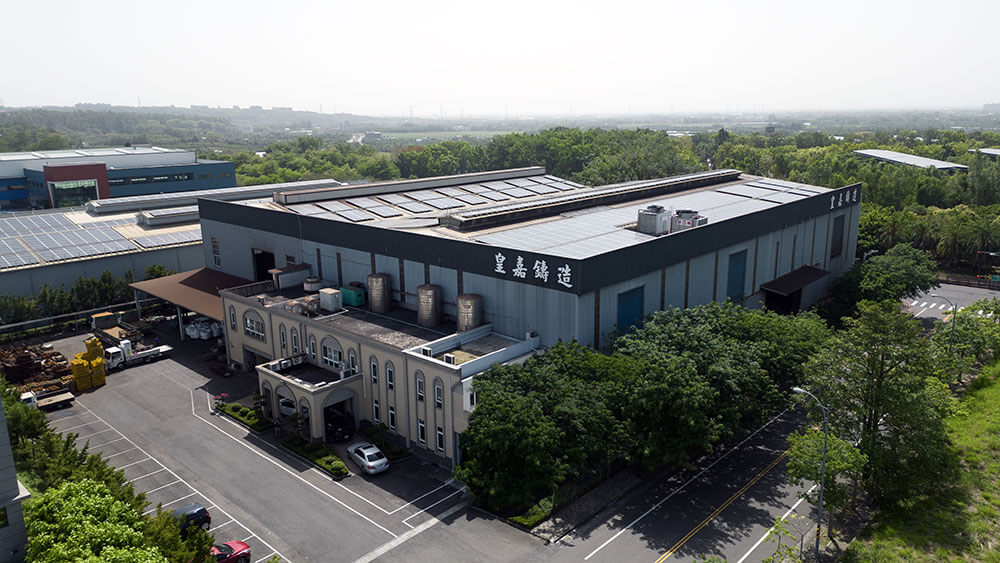
About Us Royal Metal Casting Co., Ltd.
With the rapid development of precision engineering and heavy industry manufacturing, the demand for higher metal casting quality and stability continues to grow. Royal Metal Casting Co., Ltd., leveraging years of practical experience, has built a professional and innovative casting platform. Focusing particularly on components required for high-temperature and high-pressure environments, we have introduced intelligent monitoring systems and optimized mold designs to reduce defect rates and improve overall yield. In the automotive sector, particularly in parts such as brake systems, transmissions, and engine structural components, our products have gained international recognition across Europe, America, and Asia, providing stable supply support to many automotive and construction machinery brands.
We have introduced multiple high-end equipment and intelligent manufacturing monitoring systems to help production units adjust parameters in real-time, enhancing operational stability. At the same time, our team continually improves data collection and analysis capabilities, utilizing big data and machine learning tools to accurately predict process variations, achieving higher yield rates and traceability. By integrating technology with practical application, we not only lower production costs but also strengthen the company's adaptability, creating significant value for customers across different industries.
Company Profile Founded in 1997, Royal Metal Casting Co., Ltd. is an ISO 9001 certified foundry and precision machining factory. We specialize in the casting and machining of gray iron and ductile iron. Our main products include brake drums, brake discs, flywheels, intake and exhaust manifolds, transmission housings, crankshafts, brackets, air compressor rotors, and compressor housings, which are widely used in the automotive, agricultural machinery, and general machinery industries, and are marketed worldwide.
Royal Metal provides a complete one-stop service from product development to final machining, ensuring strict raw material control and adopting fully automated production processes with robotic assistance. Our advanced mold flow analysis software supports solution design, ensuring casting quality and shortening development lead times. For labor-intensive post-processing operations, we use advanced automated grinding equipment, achieving speeds, quality, and consistency far superior to traditional manual work.
In the field of precision machining, we have over 40 years of experience, using Japanese-imported machining centers combined with in-house designed fixtures and inspection tools, maximizing production efficiency. We firmly believe that offering high-quality products, reliable delivery schedules, and competitive pricing is our goal and responsibility for sustainable development. Royal Metal Casting Co., Ltd. is your trusted partner.
Based on a solid manufacturing foundation in Taiwan and supported by a professional team, Royal Metal has successfully risen to become a leading regional metal casting provider. In addition to supplying standard products in mass production, we are capable of customizing solutions based on clients’ production line requirements, with every stage from mold development to precision machining supervised by professional technical teams.
Continuous investment in automation equipment and quality management systems is our key strategy to face international competition and ensures that every product delivers optimal performance. Choosing Royal Metal Casting Co., Ltd. means placing comprehensive trust in quality, delivery, and efficiency.
Furthermore, we have incorporated multilingual technical support and localized consulting mechanisms into our service process, enabling clients from different countries to receive fast and accurate responses. Through the integration of online platforms and global warehousing coordination, we have shortened logistics times and enhanced supply flexibility, offering strong logistical support for our products in overseas markets. This operational model deepens partnership cooperation and, over the long term, enhances our clients' overall competitiveness.